کلمات کلیدی: فلاکس تر، فلاکس خشک، گالوانیزه گرم، گالوانیزه مقاطع، وان مذاب روی، کلرید روی، کلرید آمونیوم
چکیده:
گالوانیزه به روش
فلاکس که خود در دو نوع فلاکس تر و فلاکس خشک میباشد یکی از روشهای اعمال پوشش
فلز روی در سطح قطعات فولادی میباشد. در این روش قطعه فولادی در مذاب روی غوطهور
شده و طی واکنش شیمیایی تحت تأثیر عوامل ترمودینامیکی و سینتیکی و فرآیند دیفوزیون
لایهای آلیاژی در سطح قطعه فولادی بهعنوان پوشش ایجاد میگردد. ظاهر پوشش،
ضخامت، ساختار و خصوصیات آن تحت تأثیر عوامل متعددی میباشد. یکی از عوامل بسیار
مهم در تعیین خواص پوشش میزان خیس پذیری یا آغشته شدن روی مذاب با سطح فولاد میباشد.
عوامل متعددی ازجمله تمیزی سطح قطعه کار، عناصر آلیاژی موجود در پوشش، دمای مناسب
مذاب و قطعه کار و سایر عوامل بر این موضوع اثرگذار میباشد. اعمال پوشش گالوانیزه
به روش غوطهوری در مذاب روی، تحت تأثیر زمان و پیشرفت تکنولوژی تغییرات زیادی
داشته است، بهنحویکه برخی روشها برای اشکال مختلف فولادی منسوخ گردیده و روشهای
جدید جایگزین گردیده و در حال تکامل نیز میباشد. هرچند گالوانیزه به روش فلاکس برای
ورقهای فولادی بهویژه در ضخامتهای پایین منسوخ شده است به دلیل محدودیتهای
تکنولوژیکی و قیمت و هزینه تجهیزات و ماشینآلات، این روش برای ورقهای ضخیم
فولادی همچنان در حال استفاده میباشد. روش گالوانیزه فلاکس برای قطعات ساختهشده
فولادی نظیر گاردریلها، انواع لولهها، پروفیلها، سازههای فولادی پیشساخته،
گریتینگها، مفتولها و ... همچنان رایج بوده و مورد استفاده میباشد. در این مطلب
به توضیح فرآیند گالوانیزه به روش فلاکس میپردازیم.
مقدمه:
استفاده از فلز روی بهعنوان پوششی مناسب در برابر خوردگی
از فولادها در برابر شرایط محیطی از حدود سال 1742 میلادی آغاز شده و تاکنون توسعه
یافته است. فلز روی به دلیل خواص مناسب و فراوانی آن در پوسته زمین یکی از عناصری
است که در حفاظت کاتدی از فولادها استفاده میگردد. برای مطالعه بیشتر در این
زمینه توصیه میگردد کتاب ورق گالوانیزه اینجانب را تهیه و مطالعه بفرمایید.
جزییات بیشتر در این کتاب بهتفصیل آمده است. ماهیت گالوانیزه نمودن ورقهای
فولادی با پیشرفت تکنولوژی تغییر یافت و خطوط کورهای جایگزین خطوط فلاکس گردیدند.
با ورود ورق فولادی گالوانیزه شده به عرصه خودروسازی نیز تغییرات زیادی در فرآیند
تولید ورقهای گالوانیزه و در تکامل کورههای عملیات حرارتی و آمادهسازی این ورقها
رخ داده است که هرچه به جلوتر میرویم شاهد تغییرات بیشتری نیز خواهیم بود. با
توجه به تقاضای خودروسازان به گریدهای خاص فولادی و توجه ویژه به کیفیت ظاهری و
سطحی محصولات ممکن است تغییرات بنیادین دیگری نیز در سالهای پیش رو در زمینه پوشش
گالوانیزه برای ورقهای فولادی را شاهد باشیم. ازجمله ورقهای گالوانیزه با یک رو
پوشش و روی دیگر فاقد پوشش و پوششهایی با لایههای آلیاژی خاص. با تفکیک
گالوانیزاسیون ورقهای فولادی بهویژه در ضخامتهای پایین در این مطلب به
گالوانیزه سایر مقاطع نظیر قطعات ساختهشده فولادی، لولهها، پروفیلها و غیره میپردازیم
که با روش قدیمیتر فلاکس و بهصورت کنترل شیمیایی فرآیند عملیات گالوانیزه گرم
صورت میگیرد.
تشریح فرآیند:
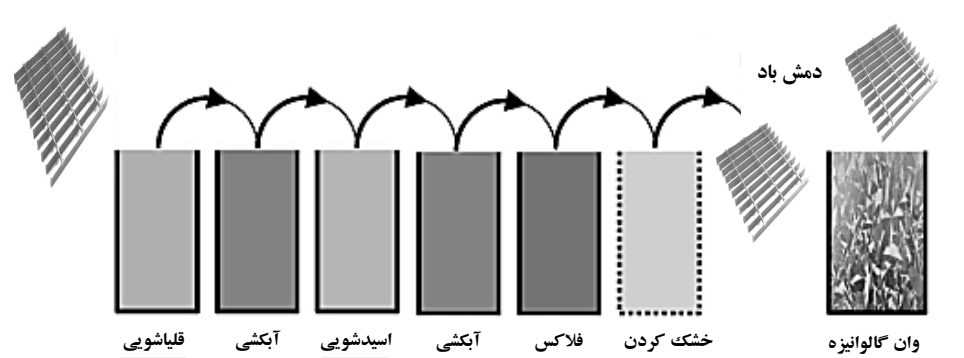
وقتی محلول فلاکس که عمدتاً شامل ترکیبات کلرید آمونیوم NH4Cl و کلرید روی ZnCl2 میباشد در تانک یا محل جدا از ذوب باشد و قطعه کار در خارج از ذوب
با فلاکس در تماس قرار میگیرد فلاکس را فلاکس خشک نامیده و در مواردی که از فلاکس
روی وان مذاب و در قسمت ورود قطعه به مذاب قرار میگیرد و درواقع فلاکس با ذوب در
تماس است فلاکس را فلاکس تر مینامند.
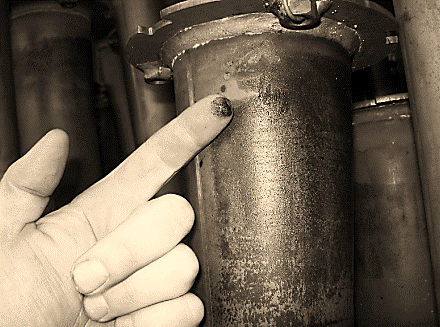
ممکن است از تعداد بیشتری از حوضچههای قلیاشویی و یا حوضچههای بیشتر آبکشی و اسیدشویی با غلظتهای مختلف در فرآیند آمادهسازی اولیه قبل از عملیات گالوانیزاسیون استفاده گردد. چنانچه شدت زنگزدگی و اکسیداسیون سطحی زیاد باشد ممکن است عملیات اسیدشویی طی چند مرحله دنبال هم صورت گیرد.
چربی زدایی عمدتاً در محلولهای قلیایی با پایه سود NaOH
و پتاس KOH صورت میگیرد. چربیهای
سطحی در واکنش با این مواد در دمای 60 تا 70 درجه سانتیگراد تجزیه و حلشده و بهصورت
سرریز همراه مواد به سیستم تصفیهخانه فاضلاب صنعتی حمل میگردند. این چربیها
حاصل فرآیندهای روانکاری و خنک کاری قبلی برای ساخت قطعات یا محافظت در برابر خوردگی
و اکسیدشدن قطعات توسط روغنهای محافظ هستند که قبل از فرآیند گالوانیزه لازم است بهخوبی
از سطح قطعه کار حذف شوند. آبکشی با آب داغ در مراحل بعدی باعث میشود قلیای
باقیمانده بر سطح شسته و پاک گردد.
فولاد و قطعات فولادی ساختهشده از آهن عموماً در سطح خود
انواع مختلف اکسیدهای آهن را به همراه دارد وجود این اکسیدها در سطح فولاد به
هنگام فرآیند غوطهوری قطعه در مذاب باعث ایجاد مزاحمت و عدم چسبندگی پوشش بر سطح
قطعه فولادی میگردد.
در خطوط گالوانیزه فلاکس از اسیدکلریدریک برای حذف اکسیدهای
آهن استفاده میگردد. اسید در غلظت در محدوده 10 تا 18 درصد با دمای 80 درجه سانتیگراد
باعث حذف اکسیدهای آهن از سطح فولاد و قطعه کار خواهد شد. معمولاً در مراحل اولیه
اسید با غلظت کمتر که حاصل استفاده در تانکهای بعدی بوده است استفاده میگردد.
اکسیدهای سطحی در سطح فولاد پایه که آهن یا Fe میباشد
به صورت لایههای مختلف ایجاد شده و روی سطح فولاد موجود است. حل شوندگی این
اکسیدها و پایداری آنها متفاوت میباشد. در جدول زیر مقایسهای از این اکسیدها
آمده است:
پایه |
فولاد پایه |
وستیت |
مگنتیت |
هماتیت |
ترکیب شیمیایی |
Fe |
Fe0 |
Fe3O4 |
Fe2O3 |
حلالیت |
سخت |
خیلی خوب |
سخت |
خیلی سخت |
در مرحله اول عملاً
لیچینگ یا خیس خوردن قطعه فولادی با سطح اکسیدی در وان اسید با غلظت پایینتر صورت
میگیرد. در مراحل بعدی سطح تمیزتر در معرض اسید تمیزتر قرار گرفته و فرآیند حذف
اکسیدها بهتر صورت گرفته و سطح تمیزتری از فولاد پایه حاصل میگردد. در این شرایط
مصرف اسید نیز بهینه بوده و عملاً اسید خالص به تانکهای انتهایی اضافه گردیده و
غلظت آنها تنظیم میگردد. اسید مصرفشده یا اسید سوخته در تانکهای ابتداییتر مورداستفاده
مجدد قرار میگیرد. دورریز اسید بهطرف تصفیهخانه اسید رفته و پس از بازیابی و
حذف آهن آن میتواند مجدداً در خط استفاده شود.
آبکشی قطعات بعد از اسیدشویی باعث میگردد یونهای
باقیمانده کلر و سایر ناخالصیها از سطح جدا گردد.
در فرآیند گالوانیزاسیون به روش فلاکس خشک، قبل از اینکه
قطعات فولادی در روی مذاب غوطهور شوند، با محلول فلاکس آغشته میگردند محلول آبی
فلاکس ترکیبی از کلرید روی و کلرید آمونیوم بوده که نسبت آن تقریباً 3 به 2 و غلطت
آن تقریباً 400 گرم در لیتر است. دمای فلاکس خشک زیر 50 درجه سانتیگراد حفظ شده و
پس از خشک شدن فلاکس در سطح قطعه کار لایه محافظی در سطح ایجاد میشود که از ادامه
اکسیداسیون قطعه کار پس از اسیدشویی جلوگیری مینماید.
وقتی قطعه آغشته به فلاکس در وان مذاب روی با دمای 450 درجه
سانتیگراد وارد میگردد کلرید آمونیوم (NH4Cl)
به آمونیاک NH3 و کلرید
هیدروژن (HCl) تجزیه میگردد.
آمونیاک بهصورت گاز از سطح ذوب خارج شده و کلرید هیدروژن، اکسیدهای روی سطحی و
آلومینیوم موجود در سطح وان مذاب را حل مینماید و تماس سطح فولاد با روی مذاب
مقدور میگردد. در این مرحله کلرید روی (ZnCl2)
موجود در فلاکس باعث کاهش کشش سطحی روی و فعال شدن سطح و شروع واکنشهای شیمیایی و
متالورژیکی میگردد که نتیجه آن ایجاد لایه آلیاژی روی آهن در سطح قطعه یا همان
پوشش گالوانیزه میباشد.
ناخالصی آهن در فلاکس اثر بدی بر سطح پوشش دارد. چون فلاکس
ماهیت اسیدی داشته و pH آن تقریباً 4.5 است
آهن را در خود تا حدودی حل میکند و بعد از مدتی در سطح مذاب سربارهای حاوی روی و
آهن وجود داشته که جمعآوری و برای بازیافت روی ارسال میگردد. شکل قطعاتی که در
وان مذاب گالوانیزه، قرارگرفته و گالوانیزه میشوند نیز بر نحوه ایجاد سرباره و واکنشهای
فلاکس همراه قطعه با سطح مذاب مؤثر است. در مواردی با افزودن آباکسیژنه یا
پراکسید هیدروژن H2O2
به فلاکس خواص بهبود یافته و آهن دو ظرفیتی به آهن سه ظرفیتی تبدیل میگردد. در
این شرایط هیدروکسید آهن نامحلول سه ظرفیتی Fe(OH)3 موجود در فلاکس بهراحتی با فیلتر پرس جمعآوری
میگردد. تنظیم pH روی عدد 4.5 اهمیت ویژهای دارد
با افزودن هیدروکسید آمونیوم (NH4OH)
یا اکسید روی (ZnO) نیز میتوان این عدد را تنظیم
نمود. افزودن پرمنگنات پتاسیم نیز همانند پراکسید هیدروژن میتواند عمل نماید در
این حالت دی اکسید منگنز ایجاد گردیده که بهصورت نامحلول همراه با هیدروکسید آهن
پشت فیلتر پرس جمعآوری میگردند.
وان مذاب در خطوط گالوانیزه فلاکس معمولاً فلزی بوده که بخش
زیادی از آن با سرب مذاب پر شده است. در واقع قطعه کار پس از آغشته شدن به فلاکس
وارد سرب مذاب شده با ماندن در سرب مذاب دمای آن افزایش یافته و به هنگام خروج از
وان مذاب از حجمی از مذاب روی که در قسمت بالای وان روی سرب بهصورت مذاب قرار
دارد عبور داده میشود. به دلیل اختلاف دانسیته سرب و روی این دو مذاب از همدیگر
جدا بوده و مذاب روی با دانسیته 6.57 گرم بر سانتیمتر مکعب روی مذاب سرب با
دانسیته 10.66 گرم بر سانتیمتر مکعب قرار میگیرد. لذا قطعه کار به هنگام خروج از
مذاب از لایهای از روی خارج گردیده و واکنشهای گالوانیزه در این لحظه اتفاق میافتد.
برای خطوط با فلاکس تر بعد از عملیات آمادهسازی قطعه روی
مذاب نیز ترکیبات فلاکس ریخته میشود و چون فلاکس در تماس با مذاب میباشد به این
روش فلاکس تر گفته میشود.
بهمنظور بهبود خواص پوشش عناصر دیگری نیز در وان مذاب
گالوانیزه افزوده میگردد که مهمترین آنها آلومینیوم میباشد. آلومینیوم نقش
کنترل رشد لایههای آلیاژی پوشش را ایفا نموده و باعث بهبود چسبندگی پوشش میگردد.
آلومینیوم در وان مذاب خطوط گالوانیزه خواص دیگری نیز دارد که برای مطالعه بیشتر
به کتاب ورق گالوانیزه مراجعه گردد.
از دیگر عناصر افزودنی به مذاب میتوان به قلع و آنیتموان
اشاره نمود. این عناصر باعث سیالیت بیشتر مذاب و بهبود وضعیت طاهری پوششهای
گالوانیزه میگردند.
بعد از خروج قطعه از مذاب بستگی به شکل قطعه عملیات بعدی
روی آن اعمال میگردد. ممکن است در قطعات کوچک قطعات برای تنظیم مقدار پوشش داخل
سبدهایی قرار گرفته و تحت نیروی گریز از مرکز در اثر چرخش سریع مقدار پوشش آنها
تنظیم گردد. در لولهها با استفاده از خط بخار و هوا مقدار پوشش داخل و بیرون لوله
تنظیم میگردد. در قطعات بزرگ با کج کردن قطعه و زاویه دادن به آن روی اضافی در
اثر نیروی ثقل و همچنین با استفاده از ابزار پوشش اضافی از زیر قطعه جمعآوری
گردد. بعدازاین مرحله با توجه به کاربرد قطعات ممکن است قطعات توسط آب خنک شده و
مورد عملیات پسیویشن یا روئین کردن واقع شوند.
گالوانیزه به روش فلاکس نیز فرآیندی کاملاً علمی بوده که
نیازمند دانش و تخصص کافی میباشد. شرکت فولاد تجهیز آران با حضور متخصصین حاذق در
این حوزه اطلاعات بسیار ارزشمندی را در اختیار علاقهمندان این صنعت میتواند قرار
دهد. برای کسب اطلاعات بیشتر میتوانید با این مجموعه در ارتباط باشید.